POWER TRANSMISSION INDUSTRIES
Products


Fluid Couplings
A fluid coupling is a transmission based on the kinetic energy of a fluid. Each fluid coupling shaft is rigidly coupled to an impeller, and between them circulates a fluid flow. The kinetic energy of the flow thrown by the driver impeller 1 is greater than the kinetic energy of the flow thrown by the driver impeller 2. The torque T transmitted by the fluid coupling is proportional to the difference of speed (slip) between the impellers.
Under operation at rated torque, the relative slip of the fluid coupling stays normally on the range 1.5% – 6.0%.
The relative slip in % of a fluid clutch is defined as 100 x (n1 – n2) / n1
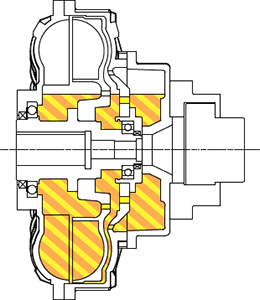
[Shutdown]
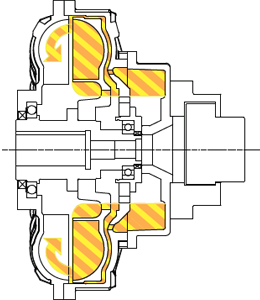
[Accelerating]
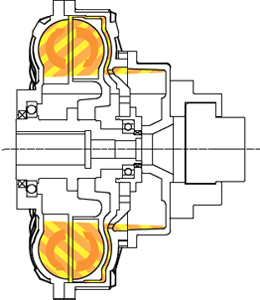
[Operating]
Operating principle
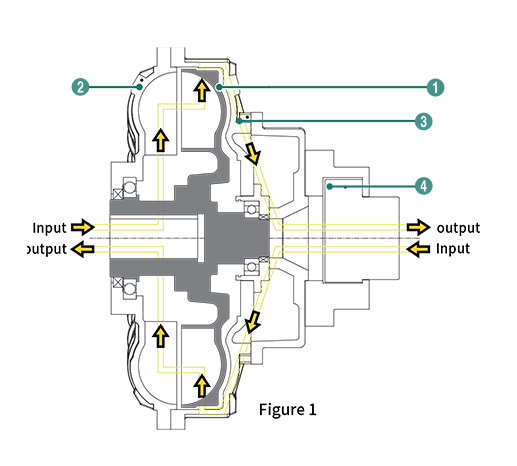
- 1. start-up impeller
- 2. driven impeller
- 3. Cover
- 4. sub coupling
Types
Standard type
- It is possible to protect driver and driven equipment from shock and vibration since there is no mechanical connection.
- It is possible to shutdown driven equipment by reversing the motor.
- It is possible to replace an expensive wound-rotor motor with a general motor.
- It is possible to distribute the load by adjusting the oil level for each motor fluid coupling in multi-motor drives.
Chamber type
Chamber type fluid coupling makes possible a very soft start or stop operation, by a gradual filling or emptying of oil from the impellers, since oil is stored in the chamber
at holding time and flows into the circuit through the nozzle during operation. And there is less slip since oil in the chamber is in the operating circuit during the constant speed operation. It can be used effectively to control the starting torque to prevent belt breakage, especially on belt conveyors.
Model
PHD/PHCD
PHF/PHCF
PHG/PHCG
PHP/PHCP
Selection of Fluid Couplings
Table for selecting specification by used power and input speed
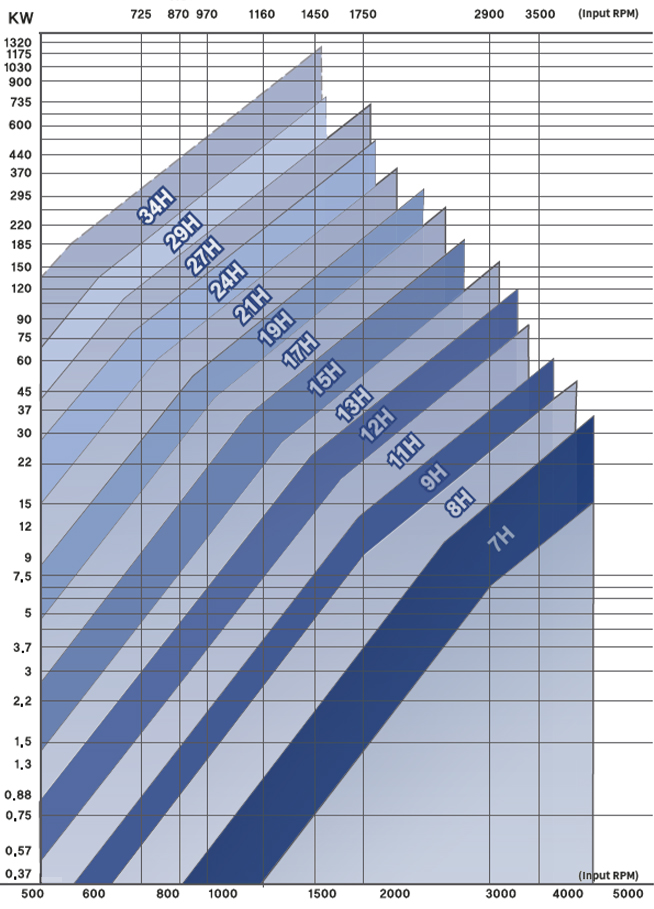